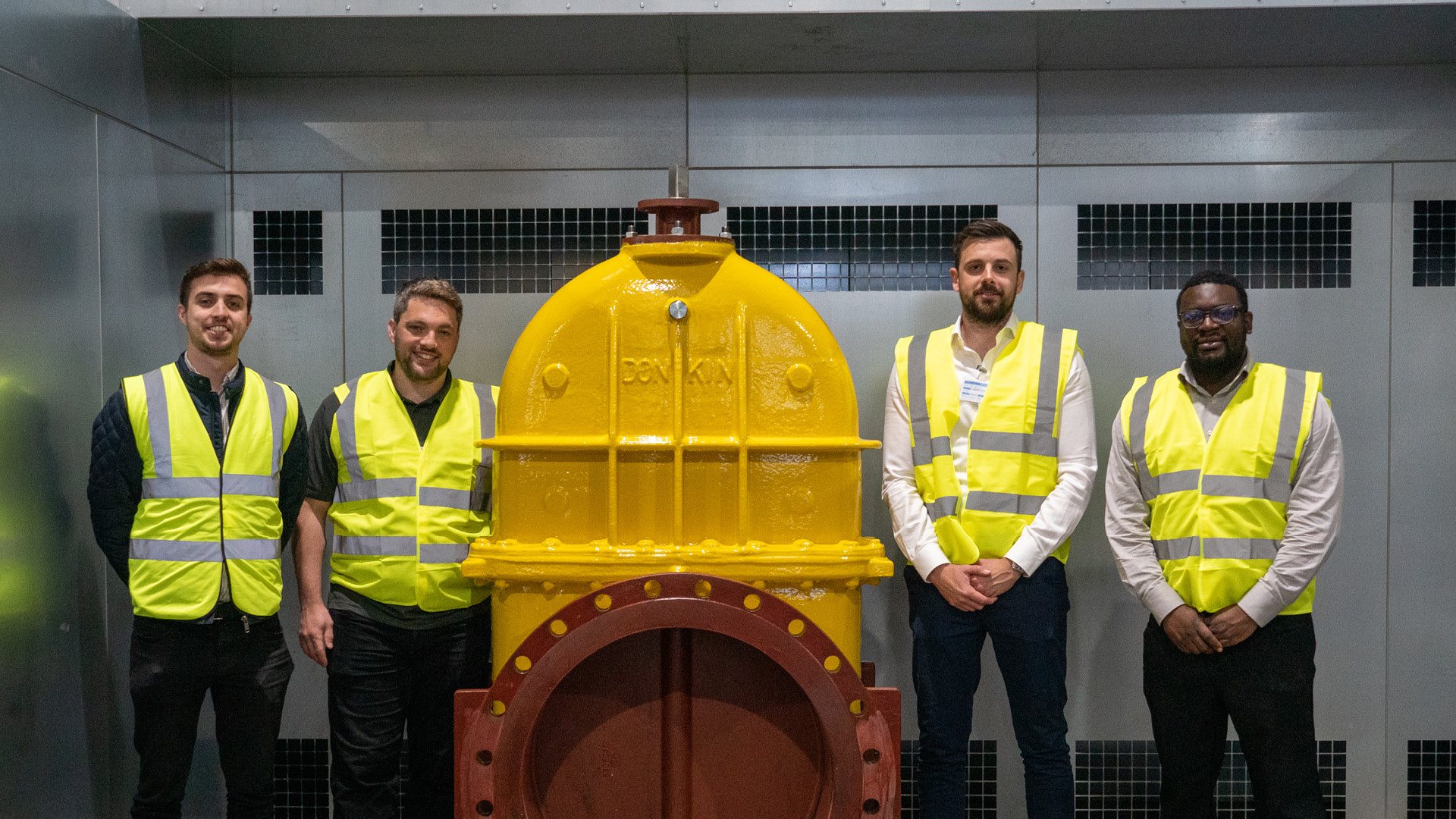
Cadent Engineers witness the Polyurethane (PUR) coating of AVK Donkin’s first large diameter DN800 gate valve
A team of senior Cadent engineers recently visited the AVK Donkin site in Staveley to witness the PUR (polyurethane) coating of two DN800 Series 555 gate valves. AVK Donkin is currently the only UK manufacturer able to supply PUR coated DN800 gate valves.
Construction of an 800mm Main
Cadent is currently delivering a longstanding commitment to increase the capacity and resilience of its medium pressure network in London; a commitment that will require a programme of works extending well into the next decade. A key element of these works is the construction of an 800mm (ring) main in North London. The new main will enable Cadent to increase the pressure and flows in that area of the network thereby ensuring that gas supply meets the needs of London’s growing population.
DN800 PUR Gate Valve Development
The 800mm main is being constructed using PE (polyethylene) pipe. Whilst 800mm pipe has been used in water networks, it is a size that is new to gas. The project in North London has required the development of both new pipes and the DN800 Series 555 gate valve.
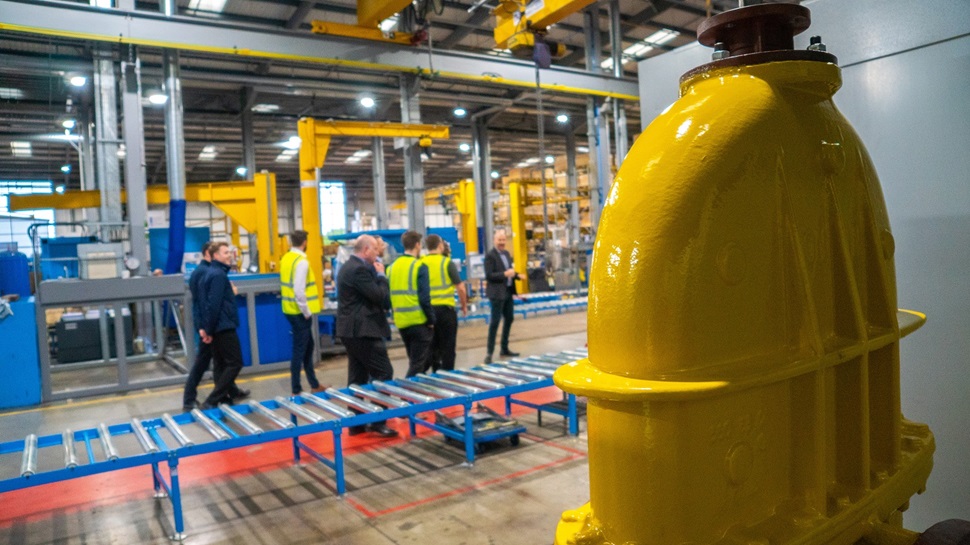
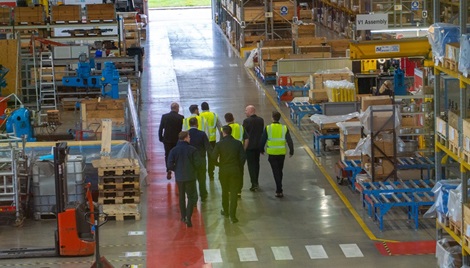
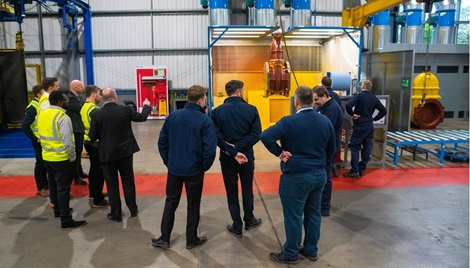
What is PUR Coating?
Protecting the DN800 Series 555 gate valve with a PUR coating delivers considerable benefits. The PUR coating protects the valve from corrosion and abrasion in its challenging environment below the streets of London.
A PUR coating can also save up to two days off the time required to install the valve. The alternative to a PUR coating is for a valve to be ‘wrapped’ during installation. Valve wrapping is a difficult and time-consuming activity requiring a far larger excavation than that needed for a PUR coated valve. The excavation has to provide sufficient space to allow the installation team to access all areas of the valve so it can be prepped and then wrapped in a waxy oil coated tape. Anyone who has travelled on the streets in London will recognise just how busy they are and the significant level of disruption and delay associated with any type of work that leads to road closures and traffic management.
Cadent Witness the PUR Coating Application
The Cadent delegate was led by Senior Project Manager, Tinashe Kambarami, along with fellow engineers Matthew Bunce, Matthew Oxley and Jack Deaney of Morrison Energy Services who between them oversee the London Medium Pressure scheme. The engineers watched the application of PUR coating to two DN800 Series 555 gate valves in the dedicated AVK Donkin coating facility. The visit coincided with the release of a Cadent Engineering Bulletin stipulating that all valves, regardless of size, should be PUR coated for buried applications.
To meet the growing market demand for PUR coated valves across all sizes, AVK Donkin has made a significant investment in additional production and coating facilities. This investment has further strengthened its capacity to deliver PUR coated valves to both UK and international clients.
The visit was arranged by Andy Hatton, AVK UK’s Sales Manager for UK gas networks:
The UK gas sector is, quite rightly, obsessed with safety and durability. The PUR coating reduces the time and complexity of valve installations, as well as extending the operational life cycle of the asset. It also significantly reduces the risk of any potential leak paths. The Cadent team spent around three hours checking out the PUR coating process which generated really interesting questions and discussions involving AVK Donkins engineering team.
AVK Donkin has long been the dominant name in the supply of valves, fittings and emergency repair clamps to the UK gas industry.
Contact Andy Hatton.
If you have any questions about our PUR valves or any of our gas products contact Andy on the number above or click on the email icon to write to him directly. Additionally you may like a factory visit with on site training - we can cater our training to suit new starters through to experienced engineers who would like a refresher - contact Andy.