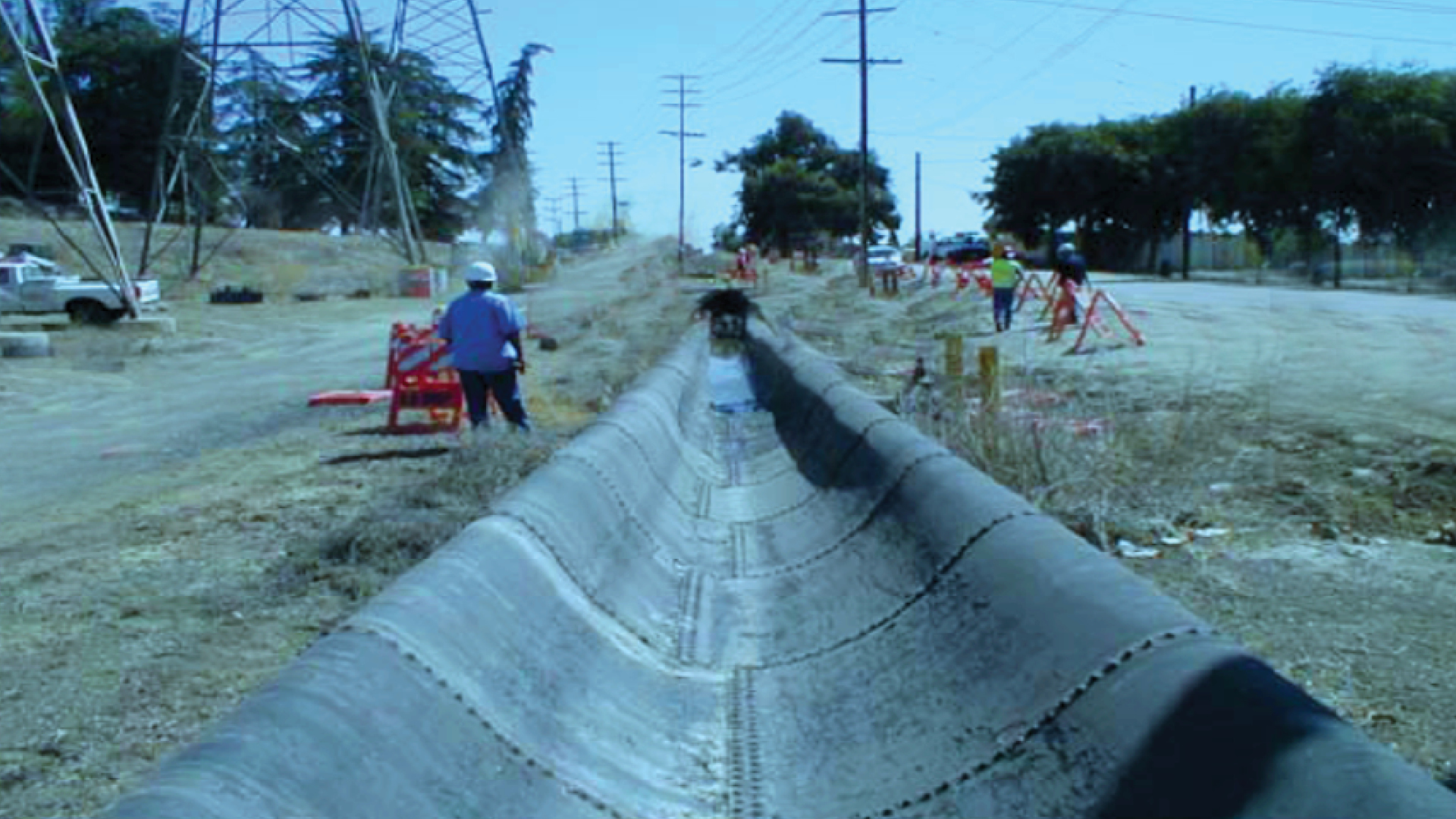
Network Safety Pipeline Vacuum Issues
Negative pressure in a pipeline causes vacuum. In extreme conditions, this causes the pipeline to implode and buckle.
What is pipeline vacuum?
Vacuum can occur in pipes due to a lack of air in the system as shown in the images above and below, causing severe irreversible issues. This can be prevented by installing air valves. Vacuum in a pressurised pipe system, can be caused by: inefficient air valves not reacting to hydraulic conditions, air valves having historically failed due to lack of maintenance and air valves being absent from the pipeline altogether. This occurrence can cause major damage to both the efficient performance of the pipeline and premature failure of the pipeline. Correctly sized and located air valves offer a solution to this issue.
Air valves are visually associated with the release of air from the system, and therefore commonly known as air release valves. However, this name is misleading as their other function, introducing air in to the system, is equally as important.
Associated common hazards
Apart from preventing the flow, the most common hazards of vacuum are:
1. Enhanced problems and damage to the pipeline causing:
- Suction of contaminants, mud and dirt through faulty connections, cracks in pipes and accessories.
- Suction of seals and gaskets, in-line fittings and other internal accessories of pipes.
- Uncontrolled suction of injected chemicals into system.
- Pipe or accessory collapse.
2. In some cases the absence of an air cushion can increase the damage of surge and slam phenomena.
3. Reduces whole life of pipe asset due to positive and negative pressures acting on the pipe wall.
This can result in fatigue loading which will weaken and eventually cause failure of the pipe wall. This is especially important on ageing assets where the pipeline material degradation is likely.
Continuous air flow
Managing air discharge in the system requires the correct level of air discharge or vacuum break to ensure that air can be drawn back into the main during negative pressure situations. In an industry with ageing assets and a desire to extend the working life, negative pressures, left un-managed, have been proven to cause additional issues that can extend to contaminated material or fluids in potable water pipelines via old joints or minor cracking of the mains.
Professor Joby Boxall in his joint report of 2015, demonstrated that three requirements that must coexist for contaminant ingress to take place within water distribution systems;
- The existence of a contaminant source external to the distribution pipe (contaminated ground water).
- A pathway providing a route into the system (failed or failing pipe joints or limited leaks).
- A driving force (negative pressures within the pipeline).
As such, to allow a system to remain unprotected from this form of contamination allows the potable water to run the risk of becoming contaminated.
One solution to this is to remove one aspect of the three requirements: the driving force. Air valves are the most efficient and cost effective tool to achieve this and by installing and maintaining a system of air valves, negative pressure is managed and removed from the equation, allowing the ageing network to remain protected.
Diagram courtesy of: Fox, Sam & Shepherd, Will & Collins, Richard & Boxall, Joby. (2015). Experimental Quantification of Contaminant Ingress into a Buried Leaking Pipe during Transient
Events. Journal of Hydraulic Engineering. 142. 04015036. 10.1061/(ASCE) HY.1943-7900.0001040.
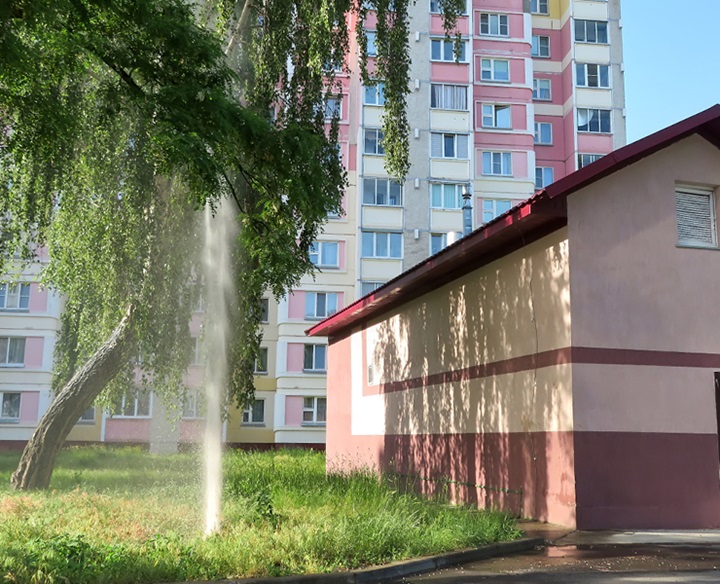
Air Release and Vacuum Issues
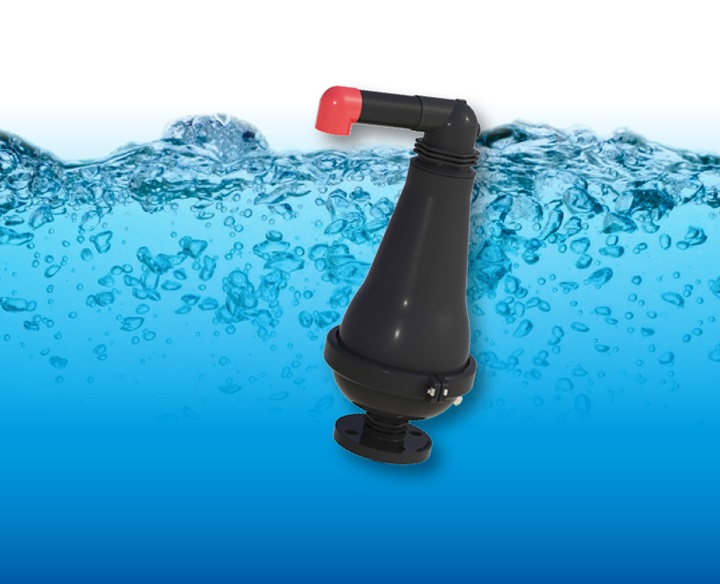
Air Release and Vacuum Solutions
Air Valves improve pipeline performance, managing air discharge, increasing system efficiency
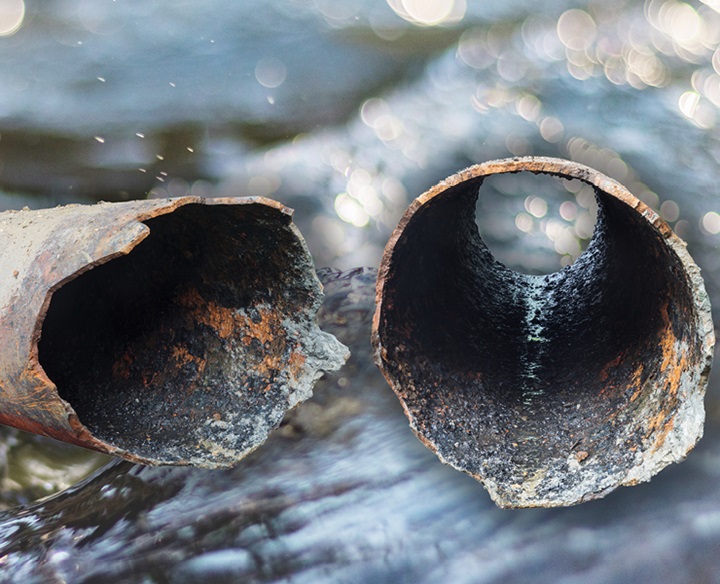
Water Hammer Issues
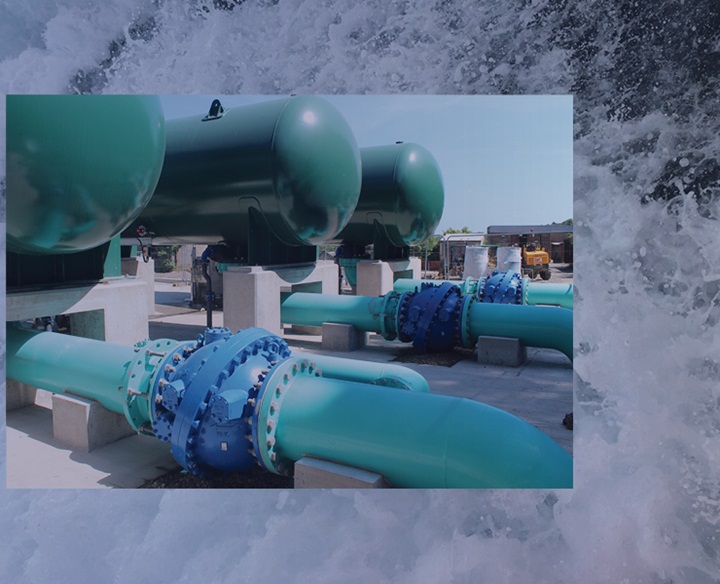
Network Safety Solutions Home Page
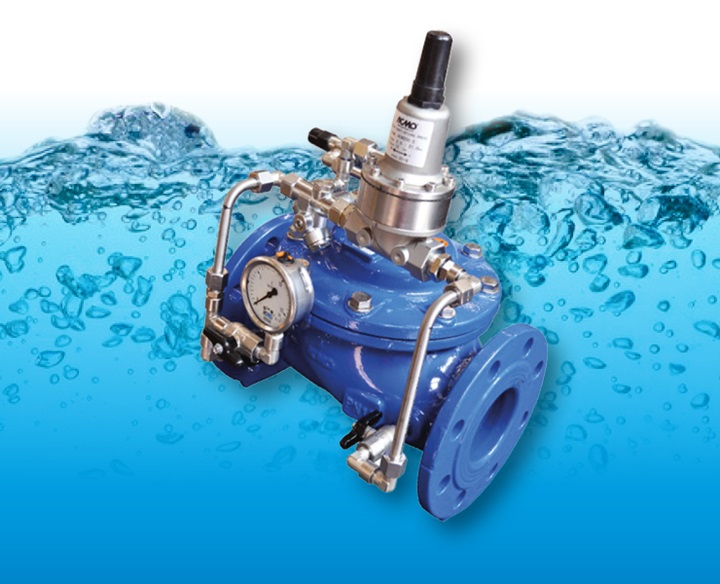
Water Hammer Control Valve Solutions
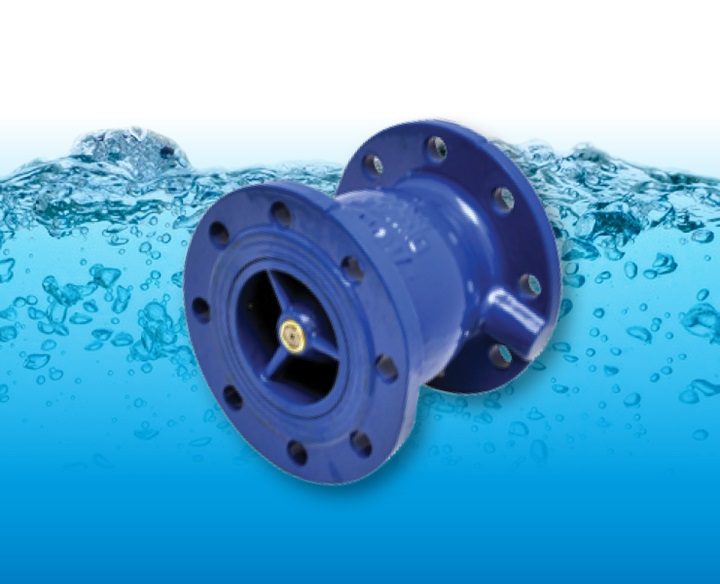