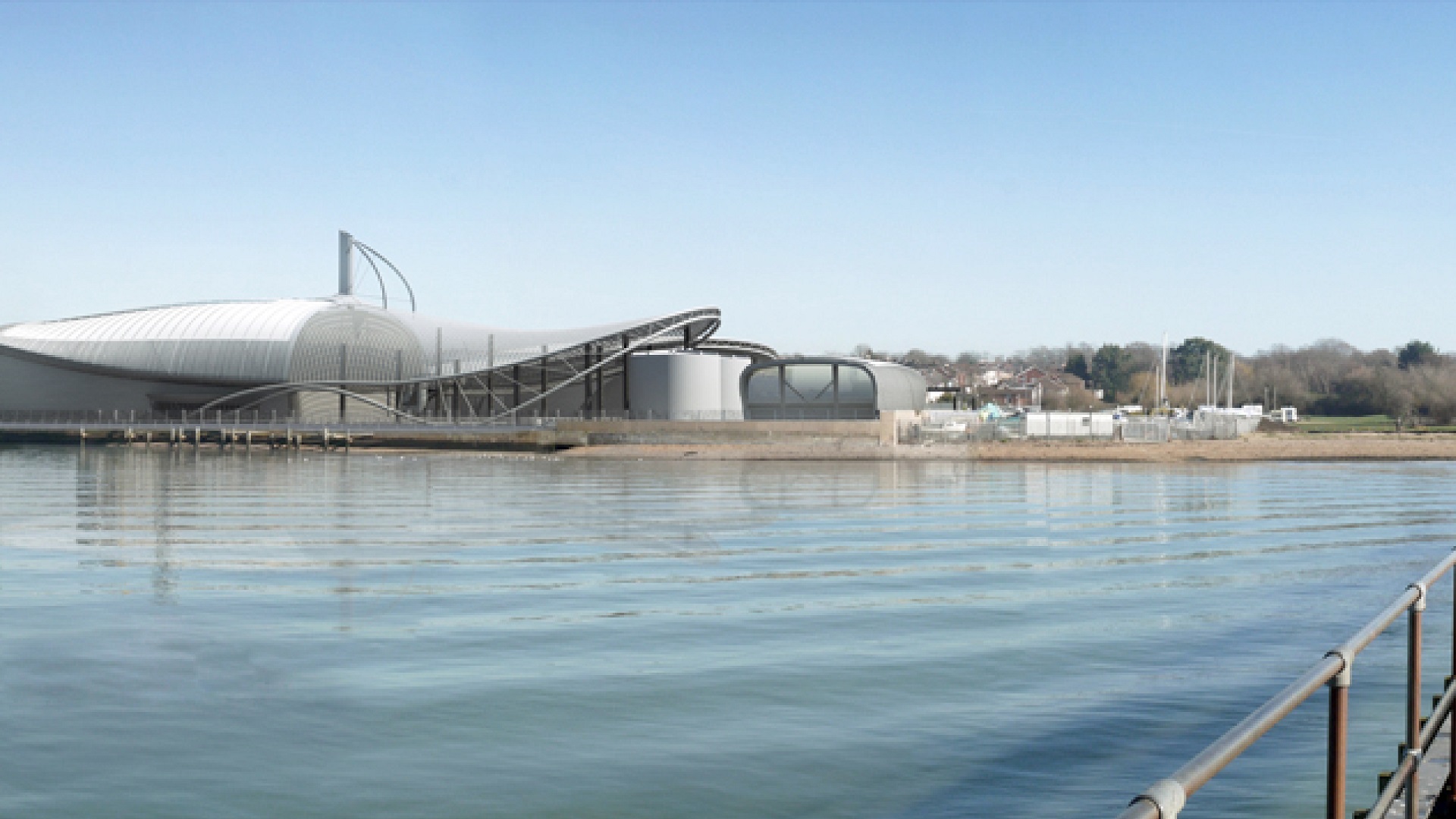
AVK UK Supply Valves, Penstocks and Stop Logs to Woolston
As a framework supplier to Southern Water, AVK UK have been supplying an extensive range of valves and penstocks to the Woolston Wastewater Treatment Works Redevelopment since 2014.
Originally built in 1966, the treatment works has been undergoing a multimillion-pound redevelopment since 2014. During the project, wastewater continued to be treated through an adjacent temporary plant whilst the new plant is designed and built. The completed project will:
- Reduce odours to surrounding areas
- Ensure the treated wastewater leaving the site meets new, higher environmental standards
- Ensure the redesigned works fits in with the ongoing redevelopment of the area
The result will be a modern wastewater treatment works that will serve the area long into the future. The new site will replace open air tanks, where the odours originate, with new treatment processes that are fully odour controlled and contained within the buildings.
The range of valves and penstocks delivered to site included:
- DN50-400 Series 21 resilient gate valves manual and electric operation
- DN100-400 Series 41 Non-return valves with Lever weight and guard
- DN150-250 Eccentric plug valve electric operation
- DN50-350 Series 75 butterfly valves electric operation
- DN50-800 Series 702 knife gate valves, manual and electric operation
- Variety of Series 772 stainless steel penstocks and stop logs as well as multitude of small diameter stainless steel ball valves
The valves were manufactured in AVK UK factories and other AVK plants across the world ensuring consistent high quality and supply chain management.
AVK Technical Solutions
AVK UK promises to offer solutions not only products as perfectly demonstrated by the sizable knife gate valves shown below. The issue was the vast distance of 3m from the centre line to the operating platform above. The standard practice would be to fit the valve with an extension stem leading to a floor mounted pillar and actuator on the operating platform.
Normally this would need the design of a costly floor structure suitable for supporting the pillar and actuator equipment. AVK’s manufacturing plant experts removed the need for a complex flooring arrangement and designed an innovative and cost-effective solution by creating a self-supporting framework mounted to the body of the valve. This bespoke design also catered for the extreme coastal environment and was delivered in a timely manner to avoid programme delays.
Product and Quality
Key to AVK’s high standard of manufacture is the robust testing procedures for all valves prior to despatch, as shown below for a Series 702 DN600 knife gate valve. Regardless of the combination of size and type of valve being supplied to Woolston, the seat is tested to 1.1 times the rated working pressure, and the body tested to 1.5 times the rated working pressure.
It was not just the product, size and scope of the valves supplied that was complex. Given the coastal location of Southern Water’s redevelopment, many of the valves supplied were manufactured to the AVK coastal specification. Amongst other features, this includes enhanced coating and increased specification of the material grades used. This ensures AVK’s valves survive the arduous atmospheric conditions and harsh environments.
To discuss your project contact Stuart Montgomery